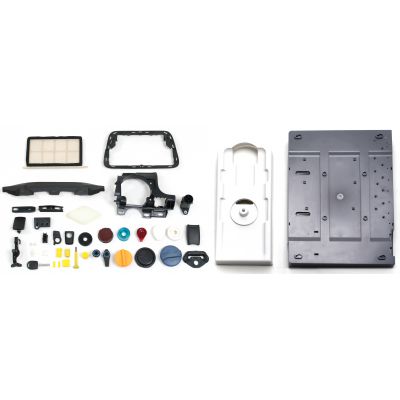
Injeção Plástica: Conheça o processo de injeção do plástico
A manufatura é um sistema de produção manual, que transforma a matéria-prima em produtos para serem comercializados. Esse processo se refere a uma grande variedade de atividades realizadas por ações humanas, do artesanato até a mais alta tecnologia, sendo essa, a mais utilizada para produções em grande escala.
O processo manual pode ser feito com a utilização de máquinas, aplicando a divisão de trabalho, onde cada operário executa a sua função no fábrica, por meio de instrumentos individuais.
O plástico é um dos materiais mais utilizados na indústria manufatureira, estando sempre em desenvolvimento, buscando aderir novas técnicas na sua produção, trazendo excelência nas fabricações.
Um dos processos mais utilizados no cenário da manufatura atual é a injeção plástica, facilitando a produção de um mesmo produto em grandes quantidades, em um curto período de tempo.
A injeção plástica é um processo que disponibiliza ao cliente um atendimento personalizado, para que se entenda com exatidão a criação do seu produto, escolhendo os tamanhos e dimensões desejadas para a elaboração.
O que é uma injeção de plástico?
A função da injeção plástica baseia-se no conceito de moldagem. É o derretimento do polímero para esculpi-lo em um molde comum para todos os produtos, a peça retirada deste molde, através da técnica de extração correta, apresenta as dimensões e tamanhos desejados.
Esse serviço passa por um processo complexo, dependendo de alguns fatores, como a temperatura, condições de resfriamento, pressão e velocidade ao injetar no material.
A origem do plástico
O plástico é uma das matérias-primas mais utilizadas no mundo, servindo para a fabricação de inúmeros produtos. Sua origem não é de recurso natural, ela veio de pesquisas e experimentos químicos, até chegar nas resinas do petróleo, matéria-prima principal para a composição do plástico, que são materiais poliméricos, ou seja, longas cadeias de moléculas formadas por unidades repetitivas.
A nafta, substância extraída do refino do petróleo, é levada para as indústrias de 1° geração, onde passam por um processo térmico chamado craqueamento, onde são quebradas em moléculas menores dando origem ao eteno. O eteno é transportado para indústrias de 2° geração, permitindo a realização da polimerização, a partir disso surgem os diferentes tipos de resinas plásticas, elas que são levadas para indústrias de 3° geração, passando pelos transformadores que dão cor e forma aos plásticos.
Esses plásticos dão origem aos produtos que consumimos no dia a dia, como frascos de bebidas, embalagens de alimentos, sacos de lixo, produtos farmacêuticos, de limpeza, tanques de combustível para veículos automotivos, tubos, conexões de encanamento e até aparelhos eletrônicos.
Classificação dos polímeros
Como solução para muitas atividades diárias, a resina plástica pode ser separada por categorias, e cada uma delas se especifica para uma finalidade em questão. É possível através da classificação dos polímeros, ter uma base para entender sobre o produto e que tipo de tratamento ele receberá. Através disso, é possível transformá-lo e categorizá-los em como: PET, PEAD, PVC, PEBD, PP, entre outros.
É pela classificação dos polímeros que é possível produzir desde utensílios simples como frascos para alimentos e bebidas, pode ajudar em um sistema operacional com a construção de peças para computador e até mesmo ser utilizada na medicina com os tubos que são utilizados para hemodiálise, tanque de combustível, telhas e muito mais.
Os polímeros são um agrupamento de monômeros que se ligam e se transformam em macromoléculas, o que dá origem a polimerização. Eles podem ser divididos em dois grupos diferentes: polímero de adição e o de condensação.
O polímero de adição na injeção plástica é feito por um único monômero através de uma reação de adição. Durante o processo de criação, elas utilizam de substâncias em suas gerações para fazer uma ligação dupla entre os carbonos. No momento de polimerização, ele quebra a ligação anterior e completa a geração com duas ligações simples.
Já o polímero de condensação feita na injeção plástica é gerado pela reação de dois monômeros diferentes através da condensação. No processo de reação, há a eliminação de uma molécula, que geralmente é a água. Neste, os monômeros não necessitam apresentar ligações duplas pelos carbonos, porém, ele precisa da presença de dois tipos de grupos funcionais distintos.
Diversos setores da indústria como o da saúde, alimentícia, construção civil e outros utilizam a resina plástica como produção de muitos materiais que são essenciais para as operações e atividades que são demandadas nos mais variados ambientes. Pode não parecer, mas a injeção plástica permite o acesso à muitos produtos comuns do dia a dia.
Para que seja possível os processos de classificação dos polímeros na injeção de plástico, é necessário fazer a reciclagem do material da maneira correta. Por possuírem características semelhantes, é muito comum haver dúvidas em relação à isso. Para evitar este tipo de problema e saber diferenciá-los na hora de reciclar, iremos especificar como fazer cada uma.
7 Categorias de resina e aplicação do plástico
PET
Este material composto por polietileno tereftalato se caracteriza por ser opaco e pela sua resistência mecânica, ele é impermeável a gases e absorve água.
Sua aplicação é feita em garrafas de bebidas, embalagem de alimentos, cosméticos, remédios, em peças de computador e engrenagens, tubos de hemodiálise, seringas e muitos outros.
O PET é um dos melhores polímeros para reciclagem, e este processo deve ser feito em passos como: separação dos materiais, limpeza, identificação do tipo de PET e, por fim, podem ser liberados para a produção de novos itens.
PEAD
O PEAD é feito de polietileno de alta densidade, em suas características é possível encontrar como no anterior um material opaco, é mais fácil de ser processado e mais resistente e com especificações mecânicas melhores. Possui resistência à substâncias químicas.
Ele é comum de ser aplicado em bolsas, cápsulas, embalagem de alimentos, rolhas, frascos, isolantes de fios, mangueiras e recipientes de combustível, tubos e caixas.
Para fazer a sua reciclagem do PEAD ele é separado e limpo para dar origem à novos frascos e tubulações. Eles são aqueles encontrados em embalagens de iogurtes, sorvetes, produtos de limpeza e brinquedos.
PVC
Este material é mais conhecido como vinil e é fabricado através do policloreto de vinila. Sua resina plástica consegue assumir diferentes formas, desde as mais rígidas até as mais flexíveis, isso é possível através dos aditivos. Ele possui impermeabilidade e é um ótimo isolante térmico, elétrico e acústico. Também é resistente ao fogo e à produtos químicos.
Suas aplicações são comuns em equipamentos que são usados no dia a dia como nos filmes, laminados, solados de calçados, brinquedos, mangueiras, tubulação para água e esgoto, fios e cabos, embalagens para remédios e muito mais.
Na reciclagem, após a sua separação, o PVC pode dar origem à mangueiras, tubulações para esgoto, cones de plástico, entre outros.
PEBD
O PEBD possui um material feito com polietileno de baixa densidade e condutividade elétrica e térmica. Ele é resistente à substâncias químicas e possui uma variedade de características mecânicas e tem capacidade de aguentar temperaturas inferiores à 60º C.
É comum encontrar este tipo de material aplicado em isolamento de fios, embalagens, garrafas, sacos, bolsas, caixas de leite, películas de revestimento, tubos de irrigação, tubulações, mangueiras, telas de sombreamento.
PP
Feito de polipropileno, a classificação do Homopolímero PP é de resistência elétrica e mecânica. Ele pertence ao grupo das poliolefinas e é produzido a partir da polimerização pela adição do monômero propileno. Ele é resistente às condições naturais ambientais que acontecem devido ao aquecimento.
O polipropileno possui diversas aplicações e é o segundo plástico mais produzido, perdendo apenas para o polietileno. Ele é muito encontrado em embalagens e rótulos, fibras e filamentos, filmes e revestimentos de extrusão.
Processo de polimerização
A polimerização é um processo químico que forma macromoléculas, elas que são originadas através da combinação de moléculas menores, mais conhecidas como monômeros. Essas moléculas menores podem ser iguais ou diferentes, e resultam na formação de longas cadeias, chamadas polímeros.
Para ocorrer a combinação dos monômeros no processo de polimerização, é preciso ter uma valência livre ou ligação química disponível em todas as moléculas.
As valências surgem conforme acontecem as quebras de ligações, sendo realizadas através de alguns fatores, como as condições externas – luz e calor, o tempo das reações – quanto maior o tempo de reação, maior será a formação de polímeros com massas molares elevadas, os catalisadores, que facilitam essa elevação e por meio de deslocamentos dos elétrons.
Processo de injeção do plástico
O processo de injeção plástica envolve o aquecimento da matéria-prima, a injeção entra diretamente no molde e ocorre o seu resfriamento. Para a realização desse processo é necessário o uso de máquinas injetoras especializadas, capazes de cumprir o ciclo para cada peça ser moldada de forma adequada.
O ciclo completo consiste no fechamento do molde, injeção do material fundido, recalque, resfriamento, abertura de molde e extração da peça. Esse processo envolve uma série de máquinas e equipamentos que devem ser operados por um profissional qualificado.
Para conseguir uma boa peça injetada é necessário ter conhecimentos básicos nas propriedades físicas e nas características de processamento do material. Os ajustes dos equipamentos nas temperaturas adequadas para o cilindro e o molde são cruciais.
Esse processo envolve uma série de máquinas e equipamentos que devem ser operados por um profissional qualificado, para garantir desempenho e qualidade no produto final.
Preparação da matéria prima
Para dar início a preparação da matéria-prima, é necessário realizar um estudo prévio sobre a resina termoplástica a ser utilizada. Cada resina é pertencente a uma família, podendo ter alguma variação no material usado na injetora.
O processo de moldagem por injeção se inicia com a preparação da matéria-prima. Os grânulos plásticos são transportados até o sistema de alimentação da máquina injetora. O material passa por um cilindro aquecido que contém uma rosca transportadora onde ocorre a fusão dos grânulos, formando uma massa plastificada.
Uma vez plastificado, o material é empurrado pela rosca para dentro do molde que possui as dimensões e detalhes da peça a ser produzida. A peça é resfriada no molde e então extraída. A extração das peças do molde pode ser manual ou automatizada.
Acabamentos posteriores são executados por operadores que também realizam a inspeção, o acondicionamento adequado (ou embalagem quando for necessário) e o transporte das peças. As peças inspecionadas e embaladas são encaminhadas para expedição ao cliente.
Sistema de alimentação da máquina injetora
O sistema de alimentação da máquina funciona com base na bucha de injeção, é através dela que tem o primeiro contato com o molde. A bucha tem uma forma cilíndrica, onde em uma de suas extremidades encontra-se um raio esférico ou cônico. Sua função é permitir que o encaixe do bico da máquina injetora com o molde de injeção seja perfeito.
Existem dois tipos de alimentação nesse sistema, a direta e a indireta. A alimentação direta ocorre quando não se tem canais de alimentação entre a bucha e a peça, permitindo que o material passe diretamente da bucha para a peça. Já a alimentação indireta acontece quando o material sai da bucha e passa por um canal de alimentação, fazendo com que chegue na peça. Essa alimentação indireta é a forma mais utilizada, pois produz um número maior de peças por ciclo.
Pressão de injeção
Para que a cavidade do molde seja preenchida com o plástico fundido, é necessário o uso de pressão de injeção. A pressão é aplicada direta ou indiretamente na máquina, com a finalidade de forçar o material plástico para as cavidades do molde.
A intensidade da pressão de injeção depende de alguns fatores, como o tipo de material utilizado, que dependendo da sua viscosidade pode ser mais difícil de preencher a cavidade por completo, influenciando na quantidade de pressão a ser aplicada. A temperatura do molde é outro fator determinante para a pressão de injeção, o ideal é iniciar a injeção com baixa pressão e ir aumentando gradualmente até obter um resultado positivo. O tempo é um dos principais fatores, é necessário controlar o tempo de injeção e de resfriamento do ciclo.
Molde
O molde da injetora plástica é feito de aço, e pode conter placas móveis ou fixas, sendo capazes de definir a estrutura da peça a ser produzida. O material final é empurrado para fora do molde através de pinos ou parafusos ejetores, realizando todo o processo de homogeneização. Para retirar parte do calor e evitar o superaquecimento, geralmente se passa água ou algum outro fluido refrigerante no material.
Para evitar o mau funcionamento do molde é necessário ter alguns cuidados com os canais de distribuição, o poço frio e as uniformidades da temperatura. Os canais de distribuição são responsáveis por transferir o material fundido do bico até as entradas das cavidades. O poço frio tem a função de absorver a frente fria do fluxo de material. As uniformidades da temperatura são responsáveis pela garantia da qualidade do produto, a temperatura interfere no acabamento da peça, nas tensões internas, na estabilidade dimensional e contração.
Outros itens podem facilitar a utilização da injeção plástica, como os sensores de pressão interna que são instalados no molde para controlar as variáveis do processo, o design review é importante para garantir que o molde saía sem nenhum defeito. É função do departamento envolvido checar a geometria do produto, seus ângulos de saída, os canais de distribuição, o sistema de controle de temperatura, as mecânicas móveis e definir um plano de manutenção preventiva.
A proteção do molde é outro fator de extrema importância, sendo feita de forma adequada, ela garante que a injeção plástica seja eficiente. Para que isso ocorra, basta que um operário verifique a posição do molde e regule sua pressão e velocidade, ao fazer isso evita-se danos ao material e tempo de manutenção.
Extração manual ou autorizada
Existem diversas formas de fazer a extração das peças de injeção plástica. É preciso conhecer o produto e entender a sua necessidade para então fazer a extração certa com os devidos cuidados. Todos os processos devem ser feitos com atenção, pois se trata de processos complexos e delicados. Muitos fatores devem ser observados, como o tipo de matéria prima a ser injetada, as regiões mais complexas como os detalhes estreitos e pouca área, as contrações, a existência de travas e os recursos disponíveis de acionamento, entre outros.
Depois que passa pelo resfriamento, o molde se abre e a placa de extração é acionada para empurrar a peça de dentro para fora. O acionamento da peça pode ser feito de forma mecânica, permitindo uma extração mais rápida e eficiente. Porém ela também pode ser feita de forma automática que expele a peça pela gravidade em um recipiente.
Os sistemas de extração de moldes mais utilizados na injeção plástica são: extração pela placa extrusora, por pinos, por camisa, extração de lâminas, ação retardada, placa extratora, por tirantes, ar comprimido e núcleo rotativo. Cada uma tem sua especificidade que deve ser considerada conforme o tipo de produto que estará utilizando e a sua necessidade.
Acabamento e inspeção
Como se pode observar, os processos de produção do plástico são bem complexos e cheios de etapas que precisam ser feitas com cuidado e atenção. Uma das mais importantes e que dá o resultado final da injeção plástica é a do acabamento e inspeção. Neles, toda a análise é necessária para estar conforme o pedido e para poder atender as necessidades com precisão.
Através da injeção plástica, é possível ter uma variedade de acabamentos que são feitos de maneira ergonômica e, ao mesmo tempo, funcional para serem utilizados sem dificuldades. Por isso, este processo precisa de uma atenção redobrada para garantir sua eficiência e qualidade. Com um polimento bem feito, o resultado do molde será satisfatório.
Para cada tipo de material do qual ele vai ser projetado para atender, existe um tipo de acabamento e inspeção. É preciso estar atento em cada detalhe para entender como deverá ser trabalhada a peça para exercer sua funcionalidade com qualidade e sem apresentar defeitos que podem vir a serem apresentados nesta etapa final do processo.
Caso o acabamento não receba a atenção necessária, ele pode apresentar problemas na estrutura dos objetos e peças feitas pela injeção plástica, o que pode afetar toda a produção. Um dos fatores que pode causar problemas é o atrito entre o plástico injetado e a superfície, o que pode irromper o processo e apresentar falhas no molde.
Existem três fatores que podem influenciar diretamente na qualidade do produto final de uma injetora, sendo eles: o molde que pode ter canais de distribuição poço frio e uniformidade de temperatura, o material que precisa de um estudo detalhado da resina termoplástica que será utilizada nele, entendendo que uma pertence a uma família e por isso possui grandes quantidade de grades e o processo que é o tempo de secagem do material e que consequentemente interfere em sua resistência final.
Além disso, é preciso considerar pontos importantes para a qualidade final do produto, como o perfil de dosagem, a contrapressão e o recalque. Estes necessitam de conhecimento e habilidade para o acabamento do molde com precisão e eficiência.
Acondicionamento e transporte
Por passar por processos complexos e que demandam muito cuidado e atenção, ao finalizar a injeção plástica ela precisa possuir um acondicionamento necessário para promover uma resistência, principalmente para fazer o transporte. As partes internas do molde são delicadas e não podem sofrer nenhum impacto que danifique a sua estrutura.
Assim como o cuidado na hora de fazer a injeção plástica, esta atenção deve ser redobrada quanto ao transporte das peças. Ele deve ser carregado até o veículo com os materiais de suporte e apoio para que não sofra quedas e danificações. Dentro do automóvel ele deve ser colocado cuidadosamente com os equipamentos necessário para garantir sua segurança e firmeza para que ele não se movimente durante o percurso.
Os aparelhos que geralmente são usados para dar o acondicionamento para as peças para então poder transportá-las são as talhas, carrinhos tartarugas, empilhadeiras e guindastes, só então ele poderá ser carregado até o veículo para encaminhá-lo ao seu destino final. Para garantir uma segurança ainda maior das peças, pode ser utilizada de filmes stretch para firmá-los, estando bem embalados e protegidos.
O que é recalque no processo de injeção?
Depois de ter a peça finalizada, inicia-se a pressão de recalque, sua finalidade é manter o material compactado até a solidificação se completar, evitando uma possível contração na peça, que pode gerar rugosidades, bolhas e dimensões fora das especificadas.
O recalque também é responsável por outra função, evitar um esforço elevado do equipamento utilizado. Se o produto for injetado e compactado apenas com pressão de injeção, essa que deve ser elevada para fazer com que a cavidade seja toda preenchida, o desgaste dos componentes hidráulicos será maior, o nível de tensão do produto também, podendo deixar as peças quebradiças e com trincas.
Para evitar qualquer tipo de problema, é recomendável o uso do recalque com a pressão menor que a pressão de injeção. Dependendo do produto, molde ou material utilizado, o tempo programado para o recalque pode ser maior, menor ou igual ao tempo de injeção.
Copolímero de etileno vinil acetato (EVA)
Oetileno-acetato de vinila, mais conhecido como EVA, é um polímero derivado do petróleo com lenta decomposição. Emborrachado, flexível e com propriedades adesivas, sua principal característica é capacidade de absorção de calor.
Composto por resinas, agentes de expansão, cargas, ativadores, auxiliares de processos e pigmentos, o EVA passa por um processo de produção de 4 etapas, a pesagem, onde os componentes e as formulações são dosadas, a mistura dos componentes, a prensagem, que origina as formas das placas e por último o acabamento.
Por ser um plástico duro, que não pode ser amolecido para ser reutilizado em novas formas, o EVA não é um material reciclável, necessitando de uma atenção maior ao ser descartado.
Com uma grande variedade de cores, densidades, tamanhos e espessuras, o EVA é muito utilizado nas indústrias de calçados, em brinquedos, placas, decorações, atividades escolares, e por ser mais leve que a água, o EVA também é utilizado como boia, flutuadores e revestimento de óculos de natação.
Copolímero de acrilonitrila butadieno estireno (ABS)
O plástico ABS é uma resina termoplástica proveniente do petróleo, formado pela copolimerização de três monômeros, a acrilonitrila – monômero sintético produzido através do hidrocarbonato propileno e amoníaco, o butadieno – alceno obtido a partir da desidrogenação do butano e o estireno – produzido a partir da desidrogenação do etilbenzeno. Cada monômero utilizado possui suas propriedades, dando origem a vários tipos diferentes de ABS, eles são aplicados de variadas formas e em diferentes segmentos.
Pelo seu preço relativamente baixo, seu material ser leve e fácil de ser moldado, o ABS é muito usado na indústria, o plástico possui propriedades específicas como boa resistência a impactos, tração e abrasão.
Ao ser comparado com outros materiais, o ABS é considerado resistente ao calor e a baixas temperaturas, podendo ser utilizado em temperaturas que variam de 20°C a 80°C.
Embora muitos as vezes nem saibam, o ABS é frequentemente encontrado no nosso cotidiano. Com o visual esteticamente agradável, altamente pigmentado de cores vívidas e saturadas, que podem variar do transparente ao opaco. Encontramos o plástico em peças de uso geral, como brinquedos, utensílios domésticos e em artigos descartáveis, peças automobilísticas e eletrodomésticos também fazem uso do ABS. Na área de construção encontramos o plástico em fios, tubos, capacetes de segurança e diversas outras coisas.
Policarbonato (PC)
Ser um termoplástico transparente, incolor e altamente resistente ao impacto, compõem as características do policarbonato. Um material de baixa densidade, boa estabilidade dimensional e ótima resistência química e térmica.
O PC pode ser aplicado em diversas indústrias, como a eletrônica – proteções e coberturas, de semicondutores – CD e DVD, construção – vitrificação, a automotiva – faróis e janelas, ópticas – lentes e vidros de inspeção e a indústria médica – descartáveis variados.
Poliuretano (PU)
Resistente à impacto e abrasão, o poliuretano, conhecido também como PU possui uma elasticidade em comparação com a borracha. Sua flexibilidade e resistência à compressão o torna essencial em aplicações de amortecimento em geral. Isto porque ele possui uma excelente adesão a metais e se desenvolve com excelência mesmo quando trabalhado com química.
O poliuretano faz parte do grupo de plásticos que possuem características de elastômero que possui possibilidade de transformação. Isso porque tem grande variação de durezas possíveis de se estabelecer na sua formação. Pode ser utilizado tanto em serviços de repuxo, como de prensa chapa.
Entre as principais características do poliuretano, estão: resistência à tração, abrasão, impacto, metais, química, dielétrica, hidrólise, propagação de rasgos; variedade de cores e tamanhos, elasticidade ao choque, absorção ao ruído, flexibilidade, aderência a materiais e muito mais. Sua aplicação pode ser feita em diferentes materiais, como em revestimentos e rodas, amortecedores, raspadores, anéis de vedação, entre outros.
Resina epóxi
A resina epóxi é um plástico termofixo que é ativado através de um catalisador. Por ser um termofixo (material que não perde calor), as resinas epóxi não perdem a rigidez, nem derretem quando são expostas ao calor, diferente de outros tipos de plástico.
É necessário misturar a resina com um agente endurecedor para que a reação ocorra. A massa durepóxi é uma das mais populares.
Resina Fenólica
A resina fenólica é um polímero termorrígido, produzido através de reações químicas de condensação entre um fenol e um aldeído. Suas formas se apresentam de forma líquida e sólida, sendo utilizadas como taquificantes.
É possível dividir as resinas fenólicas em duas classes, a resina resole, obtidas por meio do uso de altas temperaturas, com o auxílio de catalisadores alcalinos, e as novolac, sintetizadas em meio de ácidos.
Comportamento químico, alto nível de resistência, estabilidade térmica e mecânica, capacidade de agir como isolante elétrico e térmico são as principais características das resinas fenólicas. Elas podem ser utilizadas nas indústrias de pneus, borrachas, promotores e agentes de adesão, permitindo serem encontradas em revestimentos, adesivos e agentes de cura em diversos segmentos do mercado.
Este material quando utilizado para injeção plástica, possui alta flexibilidade, leveza, resistência à abrasão e produtos químicos, oxidação e possui uma variedade de formatos. Podendo ser trabalhado de diversas formas e em segmentos diferentes.
O poliuretano tem um elevado nível de elasticidade quando comparado com a borracha. Tem uma ótima resistência à compressão, sendo recomendado para aplicações de amortecimento em geral. O material é flexível e, ao mesmo tempo, rígido. Geralmente eles ficam escondidos na alvenaria e pode servir de isolamento térmico também. Além disso, ele também se apresenta em esponjas, capas de celular, compartimentos de objetos musicais, calçados e muitos outros.
Regiões de atendimento Primo Industrial
RG
- Estado do Rio de Janeiro
- Duque de Caxias
- Belford Roxo
- Petrópolis
- Itaboraí
- Barra Mansa
- Nilópolis
- Rio de Janeiro
- Nova Iguaçu
- São João de Meriti
- Volta Redonda
- Mesquita
- Macaé
- Teresópolis
- São Gonçalo
- Niterói
- Campos dos Goytacazes
- Magé
- Nova Friburgo
- Cabo Frio
- Resende
MG
- Estado de Minas Gerais
- Contagem
- Montes Claros
- Governador Valadares
- Sete Lagoas
- Poços de Caldas
- Sabará
- Varginha
- Itabira
- Belo Horizonte
- Juiz de Fora
- Ribeirão das Neves
- Ipatinga
- Divinópolis
- Patos de Minas
- Pouso Alegre
- Conselheiro Lafeiete
- Passos
- Uberlândia
- Betim
- Uberaba
- Santa Luzia
- Ibirité
- Teófilo Otoni
- Barbacena
- Araguari
ES
- Estado do Espírito Santo
- Cariacica
- Linhares
- Guarapari
- Nova Venécia
- Castelo
- Domingos Martins
- Alegre
- Guaçuí
- Mimoso do Sul
- Pinheiros
- Serra
- Vitória
- São Mateus
- Aracruz
- Barra de São Francisco
- Marataízes
- Itapemirim
- Baixo Guandu
- Iúna
- Sooretama
- Pedro Canário
- Vila Velha
- Cachoeiro de Itapemirim
- Colatina
- Viana
- Santa Maria de Jetibá
- São Gabriel da Palha
- Afonso Cláudio
- Conceição da Barra
- Jaguaré
- Anchieta
PR
- Estado do Paraná
- Curitiba
- Londrina
- Maringá
- Ponta Grossa
- Cascavel
- São José dos Pinhais
- Foz do Iguaçu
- Colombo
- Guarapuava
- Paranaguá
- Araucária
- Toledo
- Apucarana
- Pinhais
- Campo Largo
- Almirante Tamandaré
- Umuarama
- Paranavaí
- Piraquara
- Cambé
- Sarandi
- Fazenda Rio Grande
- Paranavaí
- Francisco Beltrão
- Pato Branco
- Cianorte
- Telêmaco Borba
- Castro
- Rolândia
SC
- Estado de Santa Catarina
- Joinville
- Florianópolis
- Blumenau
- Itajaí
- São José
- Chapecó
- Criciúma
- Jaraguá do sul
- Lages
- Palhoça
- Balneário Camboriú
- Brusque
- Tubarão
- São Bento do Sul
- Caçador
- Concórdia
- Camboriú
- Navegantes
- Rio do Sul
- Araranguá
- Gaspar
- Biguaçu
- Indaial
- Mafra
- Canoinhas
- Itapema
RS
- Estado do Rio Grande do Sul
- Porto Alegre
- Caxias do Sul
- Pelotas
- Canoas
- Santa Maria
- Gravataí
- Viamão
- Novo Hamburgo
- São Leopoldo
- Rio Grande
- Alvorada
- Passo Fundo
- Sapucaia do Sul
- Uruguaiana
- Santa Cruz do Sul
- Cachoeirinha
- Bagé
- Bento Gonçalves
- Erechim
- Guaíba
- Cachoeira do Sul
- Santana do Livramento
- Esteio
- Ijuí
- Alegrete
PE
- Estado de Pernambuco
- Suape
- Recife
- Jaboatão dos Guararapes
- Olinda
- Bandeira caruaru.jpg Caruaru
- Petrolina
- Paulista
- Cabo de Santo Agostinho
- Camaragibe
- Garanhuns
- Vitória de Santo Antão
- Igarassu
- São Lourenço da Mata
- Abreu e Lima
- Santa Cruz do Capibaribe
- Ipojuca
- Serra Talhada
- Araripina
- Gravatá
- Carpina
- Goiana
- Belo Jardim
- Arcoverde
- Ouricuri
- Escada
- Pesqueira
- Surubim
- Palmares
- Bezerros
BA
- Estado da Bahia
- Salvador
- Feira de Santana
- Vitória da Conquista
- Camaçari
- Itabuna
- Juazeiro
- Lauro de Freitas
- Ilhéus
- Jequié
- Teixeira de Freitas
- Alagoinhas
- Barreiras
- Porto Seguro
- Simões Filho
- Paulo Afonso
- Eunápolis
- Santo Antônio de Jesus
- Valença
- Candeias
- Guanambi
- Jacobina
- Serrinha
- Senhor do Bonfim
- Dias d'Ávila
- Luís Eduardo Magalhães
- Itapetinga
- Irecê
- Campo Formoso
- Casa Nova
- Brumado
- Bom Jesus da Lapa
- Conceição do Coité
- Itamaraju
- Itaberaba
- Cruz das Almas
- Ipirá
- Santo Amaro
- Euclides da Cunha
CE
- Estado do Ceará
- Fortaleza
- Caucacia
- Juazeiro do Norte
- Maracanaú
- Sobral
- Crato
- Itapipoca
- Maranguape
- Iguatu
- Quixadá
- Canindé
- Pacajus
- Crateús
- Aquiraz
- Pacatuba
- Quixeramobim
GO / DF
- Estado de Goiás
- Goiânia
- Aparecida de Goiânia
- Anápolis
- Rio Verde
- Luziânia
- Águas Lindas de Goiás
- Valparaíso de Goiás
- Trindade
- Formosa
- Novo Gama
- Itumbiara
- Senador Canedo
- Catalão
- Jataí
- Planaltina
- Caldas Novas
MS
- Estado do Mato Grosso do Sul
- Campo Grande
- Dourados
- Três Lagoas
- Corumbá
- Ponta Porã
MT
- Estado do Mato Grosso
- Cuiabá
- Várzea Grande
- Rondonópolis
- Sinop
- Tangará da Serra
- Cáceres
- Sorriso
AM
- Estado de Amazonas
- Manaus
- Parintins
- Itacoatiara
- Manacapuru
- Coari
- Centro Amazonense
PI
- Estado do Piauí
- Teresina
- São Raimundo Nonato
- Parnaíba
- Picos
- Uruçuí
- Floriano
- Piripiri
- Campo Maior
PA
- Estado do Pará
- Belém
- Ananindeua
- Santarém
- Marabá
- Castanhal
- Parauapebas
- Itaituba
- Cametá
- Bragança
- Abaetetuba
- Bragança
- Marituba
MA
- Estado do Maranhão
- São Luís
- Imperatriz
- São José de Ribamar
- Timon
- Caxias
- Codó
- Paço do Lumiar
- Açailândia
- Bacabal
- Balsas